A load chart serves as a reference guide for the safe operational capacities of machinery. But what exactly is it, and why is it so crucial for telehandlers?
What is a Load Chart?
Think of a load chart as your telehandler's playbook—it outlines precisely how much weight your machine can handle and how high it can go. Crafted from thorough testing and precise calculations, this chart is your blueprint for operation. It's there to direct operators on how to work within safe boundaries, steering clear of overloading risks and protecting both the operator and the machine from any potential mishaps.
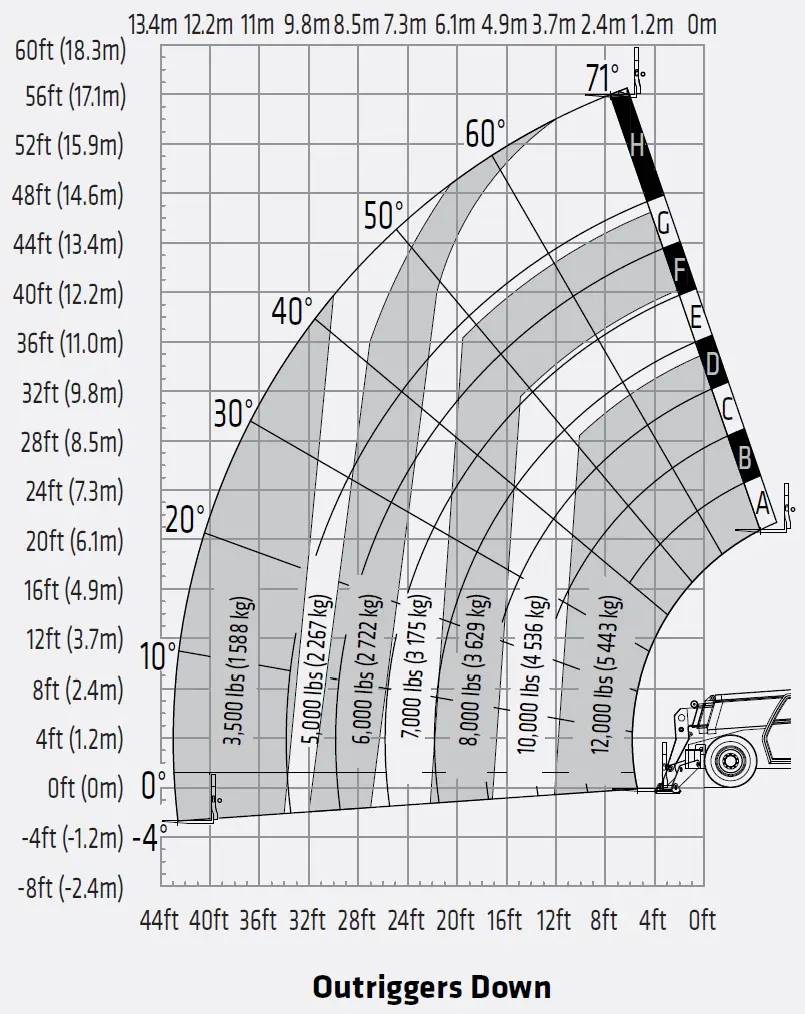
Deciphering Symbols and Terminologies
Before getting into reading the load chart, understanding these signs and terms is helpful. They provide concise information and ensure the operator can quickly determine the machine's limitations.
Common Symbols and Their Meanings:
Curved Arrows and Lines: Indicates the movement or rotation the machine allows.
Straight Arrows and Lines: Often used to denote the direction of the boom's movement.
Shaded Areas: Typically used to distinguish between safe operational zones and risk zones.
Specific Terms to Be Familiar With:
Rated Capacity: The telehandler's maximum weight is designed to lift safely under specific conditions. It's crucial never to exceed this weight limit.
Working Radius: This term refers to the horizontal distance from the telehandler's rotational center to the load's center. The working radius is vital in determining the machine's lifting capacity.
Boom Angle: This angle represents the boom's inclination relative to the horizontal plane. It's a critical determinant of the lifting capacity, with different angles allowing for different weights.
Stability Basis: The conditions under which the manufacturer conducts tests to determine the machine's safe lifting capacities. Operators should ensure their working conditions align with the stability basis mentioned in the load chart.
Outriggers: These are stabilizing structures extending outward from the telehandler's base. They stabilize the machine, especially during lifting operations with a fully extended boom.
Load Moment Indicator (LMI): This system provides real-time data about the telehandler's operating state, including weight lifted, boom angle, and length. It alerts the operator if any parameter exceeds the safe limit.
Practical Application: A Step-by-Step Guide
Reading a telehandler load chart, like the one below, is essential for ensuring safe and efficient operation.
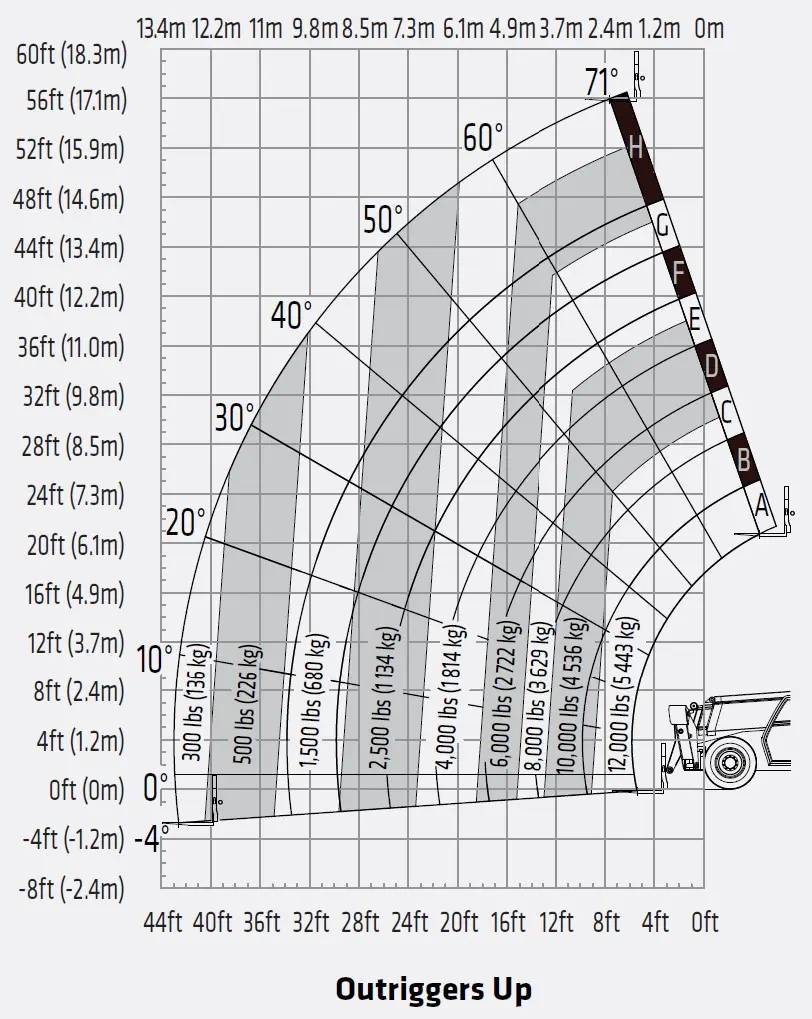
Identify Outrigger Position: This chart is specific to operations with the "Outriggers Up." Always ensure your machine's outriggers are in the position the chart specifies.
Vertical Axis - Height: The left side of the chart (vertical axis) shows the boom height in feet and meters. This is the height to which the boom can be extended.
Horizontal Axis - Radius: The bottom of the chart (horizontal axis) indicates the horizontal distance or reach from the telehandler to the load.
Load Capacities: Inside the grid, you'll notice lines labeled with different weight capacities, from 300 lbs to 12,000 lbs. These lines indicate the maximum safe weight the telehandler can lift at various heights and reaches. For example, at a 20ft height with a reach of 24ft, the maximum load capacity is just over 6,000 lbs.
Boom Angle Indicators: The angled lines labeled with degrees (10°, 20°, etc.) represent the angle at which the boom is extended. Notice how the capacities change as the boom's angle changes.
Safety Zones: The chart is divided into different zones labeled A to H. As a rule of thumb, areas closer to the machine (like Zone A) can handle heavier loads, while areas further away or at greater heights (like Zone H) can manage lighter loads. Always ensure your operations remain within these designated zones for the weight of the material you're handling.
Cross-Reference: When operating, always cross-reference the desired height and reach with the weight of the load you're handling. If the weight exceeds the specified capacity for that height and reach, adjust your operation accordingly.
Machine Illustration: The illustration at the bottom right gives a visual representation of the telehandler's position in relation to the boom's extension and angle.
Analyzing Capacity and Range
When operating a telehandler, ensuring that the machine stays within its safe lifting capacity is one of the most important things you can do. Here's how to determine and understand its lifting capabilities.
Locating the Maximum Weight
The load chart will clearly list the maximum weight the telehandler can lift at specific boom lengths and angles. Always ensure the weight of the lifted material is within this specified limit.
Boom Extension and Load Capacity Relationship
The lifting capacity often decreases as the boom extends further from the telehandler. This is due to the shift in the machine's center of gravity and the increased moment (torque) caused by the weight being further from the pivot point. Referring to the chart when extending the boom is essential to ensure the lifted weight remains within safe limits.
Factors Influencing Capacity
Other factors, like the working radius and boom angle, can also influence lifting capacity. The lifting capacity can decrease as the working radius (distance from the machine's pivot to the load's center) increases. Similarly, as previously mentioned, the angle of the boom can affect the lifting limit.
Considering Attachments
The type of attachment being used can influence the lifting capacity. Different attachments have different weights, which must be factored into the total weight lifted. While it might seem obvious, the weight of the attachment itself must be factored into the total load being lifted. Different attachments, whether buckets, forks, or platforms, have varying weights. Neglecting to account for this can lead to overloading the telehandler.
Dynamic vs. Static Loads
It's also worth noting that moving (dynamic) loads, like a swinging pallet, can exert more force than static loads, potentially impacting the safe lifting capacity. Always ensure loads are stable and secure before lifting.
Cross-Checking with Real-Time Systems
Modern telehandlers often come equipped with Load Moment Indicators (LMIs) that provide real-time feedback on the weight being lifted, the boom's angle, and length. While the load chart is a foundational reference, the LMI is a crucial real-time check, especially when working close to the machine's limits.
Considering External Factors
Running a telehandler isn't a one-man show; it's all about where you are and what's happening around you. You're working in the thick of it, where all sorts of factors can play into how well and safely your machine does its job.
Ground Conditions
Just like you wouldn’t put all your weight on a wobbly ladder, you can’t trust a telehandler on shaky ground. The wrong surface can throw off your whole game, especially with a heavy load on the line, whether it's soft soil or a lumpy landscape. Before you lift a thing, make sure the earth beneath you is solid and ready to back you up. Use your outriggers to keep things steady. And whenever you’ve got the option, find level ground—it’s always your best bet for a smooth lift.
Wind and Environmental Factors
Wind is a real challenge when hoisting heavy stuff with a telehandler. A hefty breeze can turn that load into a pendulum, and that's not a ride anyone wants. Always watch the weather report and avoid lifting when the wind's got too much gusto. And don't get me started on rain or snow; they can turn a clear day's work murky and slick in a heartbeat. Bottom line: when Mother Nature's in a mood, it pays to play it safe.
Dynamic Loads
In the operation of a telehandler, the unexpected jerks and jolts, like a swinging load or a sudden move, can add extra strain, often more than the load's weight. Before you start moving, double-check that your load is secure. And remember, it’s about precision, not speed – gentle and controlled movements maintain stability and keep everything on track.
Operating Altitude
If you're working at high altitudes, the machine's performance can differ due to changes in atmospheric pressure. Always consult the manufacturer's guidelines if operating in areas with significant altitude variations.
Temperature and Climate
When temperatures change, it's not just us feeling the heat or the chill—your telehandler does too. Blazing summers and freezing winters can mess with its hydraulics, tire pressure, and even the stuff you're hauling. Keep a regular check on your gear as the weather swings, and remember, things like metal and fluids will act up when the temps get wild. A little extra TLC for your machine can go a long way in keeping operations smooth, no matter the weather.
Safety Margins and Their Importance
What is a safety margin? Safety margins are your telehandler's built-in buffer zone. They keep you clear, ensuring you work within the machine's comfort zone and not push it too far. Even when the unexpected pops up or there's a tiny misstep, these margins can save the day. Let's examine why these safety margins are the unsung heroes of any lifting job.
Critical Importance of Safety Margins
Telehandler operations involve many dynamic and changeable factors. Sudden wind gusts, shifts in load weight distribution, or unexpected ground movement can all change the machine's balance. A safety margin ensures that the telehandler remains stable and safe even with these unpredictable variables. It acts as a buffer against the unknown and provides an extra layer of security in operations.
Gross vs. Net Capacities
Gross Capacity: This is the total weight a telehandler can lift when considering only the machine's specifications and ignoring other influencing factors. It's the theoretical maximum without accounting for safety margins.
Net Capacity: This is the weight a telehandler can safely lift and the weight the operator needs to use when you factor in safety margins. It's the real-world operational limit that takes into account the various external influences and the need for that extra buffer.
Balancing Efficiency with Safety
Tempting as it may be to push your telehandler to its max capacity to get more done, that's playing with fire. Cutting corners on safety margins for a bit more lift or reach can backfire with accidents, busted equipment, or injuries. It's all about the long game—keeping things safe today means no downtime tomorrow.
Load charts typically provide information on the net capacities, factoring in safety margins. However, always be sure you're looking at the right figures and understand the difference between gross and net capacities. Misinterpretations can lead to unsafe operations.
Common Mistakes to Avoid
- Misunderstanding or disregarding the specified capacity can lead to dangerous situations. Don’t overload!
- Neglecting environmental and ground conditions factors can affect the machine's stability and safety.
- Forgetting to account for the weight of attachments can lead to accidental overloading.
Ready to use a telehandler load chart?
Knowing how to read a telehandler load chart is a must-have skill for any telehandler operator—it's the backbone of safe and efficient operation. These charts are like the ultimate instruction manual, showing you how to work the machine no matter the job. Miss a detail, and you're in the danger zone.
Since no two telehandlers are exactly the same, their load charts are custom-made to match. Make sure you're checking the right chart for your model every time. When you're out there with this do-it-all machine, that chart is your golden ticket to getting things done right and keeping it safe. Safety first, always stay sharp with your skills, and treat that load chart like a prized possession.
Disclaimer: The information provided in this blog about telehandler load charts is intended for general informational purposes only and is not a substitute for professional operator training or certification. While we aim to help readers understand what load charts are and how they are used, this content should not be considered as comprehensive guidance for operating telehandlers or any other heavy equipment. Proper training and certification from accredited institutions or authorized training providers are essential for the safe and effective operation of telehandlers. We strongly advise all operators and industry professionals to undergo formal training and certification processes and to always refer to the specific manufacturer’s guidelines and safety protocols.