
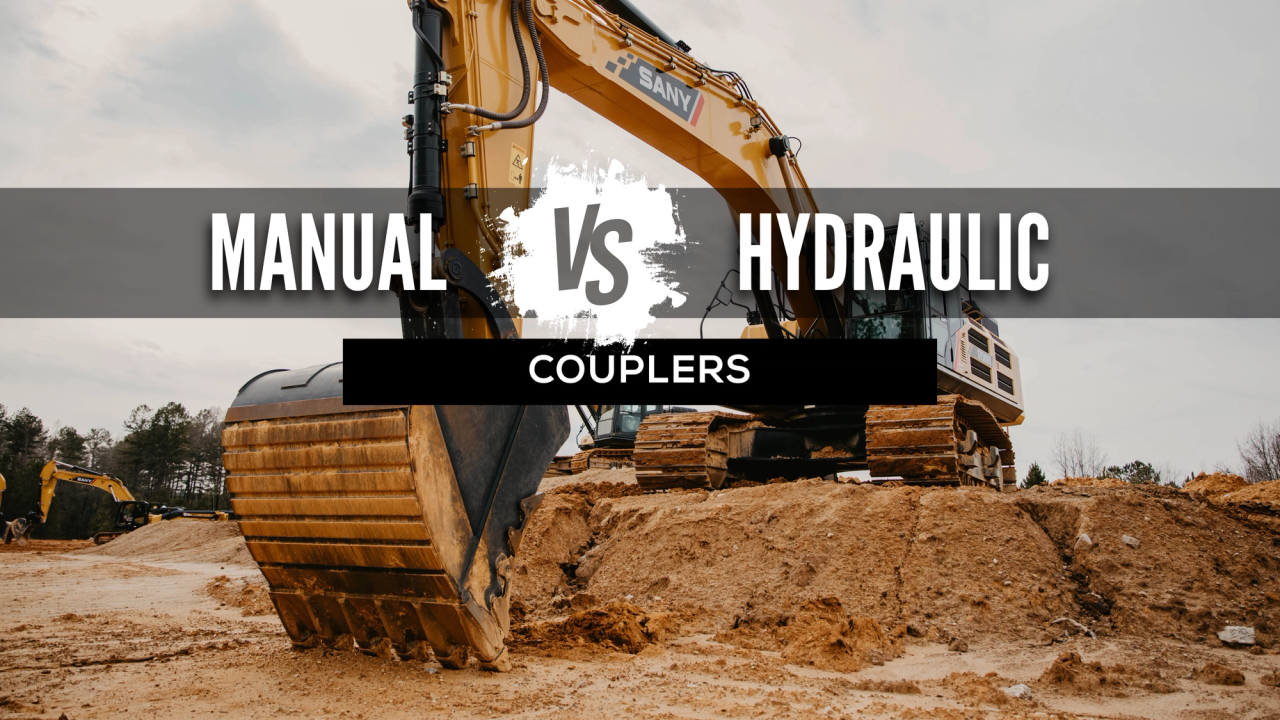
- Switching attachments quickly means less downtime and more work done in a day.
- Using a coupler reduces manpower for the task of switching out attachments. Beating out pins takes time.
- With a coupler, one excavator can do many jobs, from digging to demolishing, by simply changing attachments.
- Changing attachments with a coupler is safer for operators, as it reduces the risk of manually switching tools.
- Manual couplers are simple in design, with fewer moving parts, making them really reliable.
- They’re generally less expensive than hydraulic couplers, both in initial cost and maintenance.
- Some operators prefer manual couplers for the control and assurance of physically securing the attachment.
- The smallest minis can’t run a hydraulic couple without additional plumbing, so a manual coupler is a straightforward solution.
- Changing attachments requires manual labor, which can be strenuous and time-consuming.
- Manual attachment change can pose safety risks, particularly with heavier attachments or in less-than-ideal weather conditions.
- Manually changing attachments can increase downtime, especially in projects requiring frequent attachment switches.
- A coupler adds weight and will change the balance and reduce lift capacity.
- Easily change attachments from the safety and comfort of the cab.
- Significantly reduces downtime between attachment changes, enhancing productivity.
- Enables multiple attachments in a single project, making the excavator a more versatile tool.
- Reduces the risk of injury associated with manual attachment changes.
- Hydraulic couplers are more expensive than manual ones in terms of initial investment and potential maintenance. However, their increased efficiency and reduced downtime often offset this cost.
- You're paying for a luxury if you’re not changing attachments often.
- The added complexity of the hydraulic system means there's more that can potentially require maintenance.
Machine | Weight (in pounds) | Hydraulic Coupler | Manual Coupler |
---|
SY16C | 4,023 | | ✔ |
SY26U | 6,085 | | ✔ |
SY35U | 8,499 | ✔ | ✔ |
SY50U | 11,684 | ✔ | ✔ |
SY60C | 13,448 | ✔ | ✔ |
SY75C | 16,050 | ✔ | ✔ |
SY80U | 19,401 | ✔ | ✔ |
SY95C | 20,238 | ✔ | |
SY135C | 32,783 | ✔ | |
SY155U | 35,274 | ✔ | |
SY215C | 51,919 | ✔ | |
SY225C | 54,013 | ✔ | |
SY265C | 59,525 | ✔ | |
SY364C | 80,910 | ✔ | |
SY6500H | 120,152 | ✔ | |
- Consider the nature of your projects. A manual coupler should do the job if your work involves repetitive tasks requiring minimal attachment changes. A hydraulic coupler will save time and labor for diverse (or predictably unpredictable) projects demanding frequent switches between attachments. Hello, productivity!
- Hydraulic couplers are more expensive upfront and may have higher maintenance costs than manual couplers. Manual couplers are a cost-effective choice if budget constraints are tight, provided they meet your project's needs. However, consider the long-term productivity gains and potential cost savings from reduced downtime with hydraulic couplers.
- And like we said, the size of your excavator can significantly influence the practicality of manual vs. hydraulic couplers. Small excavators can often operate effectively with manual couplers, while large excavators benefit from the ease and safety of hydraulic systems.
Date: 05.13.2024